在柔性印刷电路板(FPC)的应用中,折弯处的柔韧性与可靠性至关重要。合理运用 FPC 折弯机,并优化相关工艺,能够有效提升 FPC 折弯处的这些关键性能。 优化折弯工艺参数
压力调控:精确的压力控制是提升 FPC 折弯处性能的基础。压力过大,会过度挤压 FPC,导致内部线路受损,降低柔韧性与可靠性;压力过小,则无法使 FPC 达到预期的折弯角度。需依据 FPC 的材质、厚度以及具体的折弯设计要求,通过反复试验确定最佳压力值。例如,对于厚度为 0.15mm 的聚酯(PET)材质 FPC,在进行 90° 折弯时,适宜的压力可能在 8 - 12N 之间。通过压力传感器和反馈控制系统,可实时监测并调整压力,确保每次折弯压力的一致性。
速度优化:折弯速度对 FPC 折弯处的应力分布有显著影响。过快的速度会使 FPC 瞬间承受较大应力,容易在折弯处产生裂纹,降低可靠性;过慢的速度虽能减少应力集中,但会影响生产效率。一般而言,适中的折弯速度在 5 - 10mm/s 较为合适。同时,可采用变速折弯的方式,在折弯起始和结束阶段适当降低速度,以缓解应力突变,提升折弯处的柔韧性与可靠性。
选择合适的模具
模具材质:模具材质直接关系到 FPC 的折弯质量。应选用硬度高、耐磨性好且表面光滑的模具材质,如合金钢或钨钢。这些材质能有效减少模具与 FPC 表面的摩擦,降低 FPC 表面划伤的风险,从而提高折弯处的可靠性。同时,良好的耐磨性可保证模具在长时间使用过程中保持稳定的形状和尺寸精度,确保 FPC 折弯角度的一致性。
模具形状与尺寸:模具的形状和尺寸需与 FPC 的折弯要求精确匹配。例如,对于半径较小的弧形折弯,应采用具有相应曲率半径的模具,以保证 FPC 在折弯过程中受力均匀,避免局部应力集中。此外,模具的尺寸精度要控制在较高水平,如模具的公差范围应控制在 ±0.05mm 以内,确保 FPC 折弯处的形状精度和稳定性。
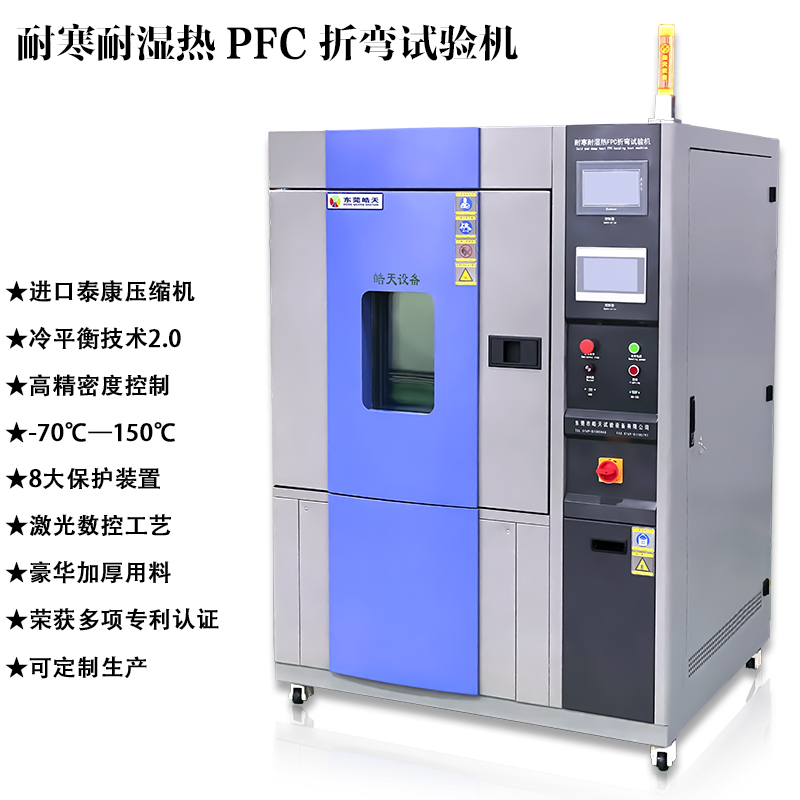
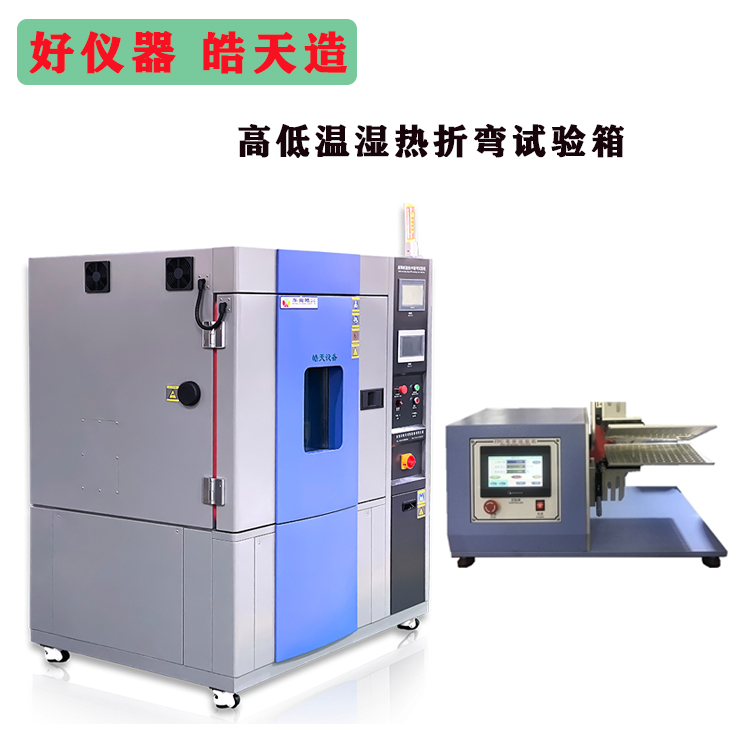
折弯前预处理与折弯后处理
预处理:在折弯前,对 FPC 进行适当的预热处理,可有效降低材料的脆性,提高其柔韧性。例如,将 FPC 在 60 - 80℃的烘箱中预热 10 - 15 分钟,使材料分子链的活动能力增强,在折弯过程中能更好地适应变形,减少裂纹的产生。此外,对 FPC 表面进行清洁处理,去除灰尘、油污等杂质,可避免这些杂质在折弯过程中导致应力集中,提高折弯处的可靠性。
后处理:折弯后,对 FPC 折弯处进行应力释放处理。可采用低温退火的方法,将 FPC 在一定温度(如 50 - 70℃)下保持 30 - 60 分钟,使折弯处的内部应力得到缓解,从而提高柔韧性和可靠性。同时,在折弯处涂覆一层保护胶,如 UV 固化胶或三防漆,可增强折弯处的机械性能和耐环境性能,进一步提升其可靠性。
通过优化 FPC 折弯机的工艺参数、选择合适的模具以及做好折弯前后的处理工作,能够显著提高 FPC 折弯处的柔韧性与可靠性,满足日益严苛的电子设备制造需求。